在制造业中,工厂质检人员肩负着确保产品质量的重任。他们需要在快节奏的生产环境中,准确无误地检查每一个产品,记录数据,并确保质量问题得到及时解决。然而,质检人员在日常工作中面临着众多挑战!
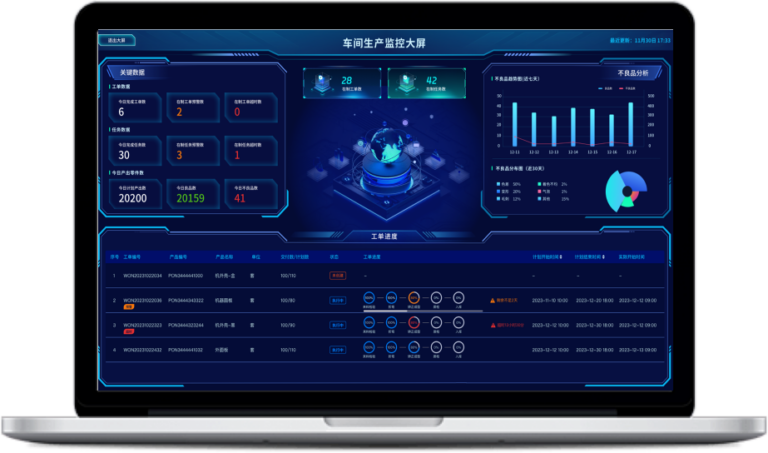
数据记录与跟踪难题
质检过程中需要记录大量数据,包括尺寸、重量、外观等。手工记录不仅效率低,而且易出错,导致数据追踪和分析困难。此外,纸质记录的存储和检索也存在问题,既占用空间,又不便于快速查询和统计。
信息孤岛与协作障碍
质检数据往往分散在不同的部门和系统中,形成信息孤岛。这阻碍了部门间的信息共享和协作,影响了整体的响应速度和决策效率。例如,生产部门、质检部门和销售部门之间的信息不同步,可能导致生产计划的调整滞后,或者客户投诉的处理延迟。
资源配置与优先级判断
由于缺乏有效的工具和数据支持,质检人员在资源配置和优先级判断上往往依赖经验,难以做到精确和科学。例如,质检人员可能无法准确判断哪些产品或批次的质量风险更高,需要投入更多的资源进行检测;或者哪些产品可以快速放行,以提高生产效率。
响应机制与持续改进
质量问题的响应和处理流程通常缓慢,缺乏快速反应机制。同时,持续改进的质量管理体系难以建立和执行。例如,当发现质量问题时,可能需要经过多个部门的沟通和协调,才能采取措施,这导致问题处理的延迟。另外,质量问题的原因分析、纠正措施的制定和执行,以及效果的跟踪和评估,都需要系统化、标准化的管理。
为了解决这些问题,许多工厂开始引入“轻量级生产管理系统”,这类系统专为中小工厂量身定制,以低成本、简洁易用的特点,提供全面的质检管理解决方案:
- 分级质检:可以根据客户和生产实际情况,自由安排首检、巡检、出入库质检、外协质检等质检项目。
- 自动化数据记录:系统通过自动化工具快速收集质检数据,减少人为错误,提高记录的准确性和效率。同时,电子化的数据存储和检索,便于快速查询和统计分析。
- 信息共享平台:打破信息孤岛,建立统一的质检信息共享平台,实现跨部门的实时数据共享和高效协作。例如,生产计划的调整、质量问题的处理等信息,可以实时推送到相关部门,提高响应速度。
- 智能资源配置:利用系统提供的数据分析和预测功能,帮助质检人员进行更科学的资源配置和优先级排序。例如,系统可以根据历史数据和实时数据,预测哪些产品或批次的质量风险更高,需要优先检测。
- 快速响应与持续改进:建立质量问题的快速响应机制,同时通过系统反馈实现质量管理的持续改进和优化。例如,系统可以自动记录质量问题的原因分析、纠正措施的制定和执行,以及效果的跟踪和评估,形成闭环管理。
引入轻量级生产管理系统,工厂质检人员可以更加高效、准确地完成质量控制任务,提升产品质量,增强企业的市场竞争力。这种系统通过全流程的数字化管理,助力工厂实现生产过程的透明化、智能预警监控以及生产工序的协同,从而全面提升质量管理水平。