304 vs. 316 Stainless Steel: A Comprehensive Material Analysis for Your Projects
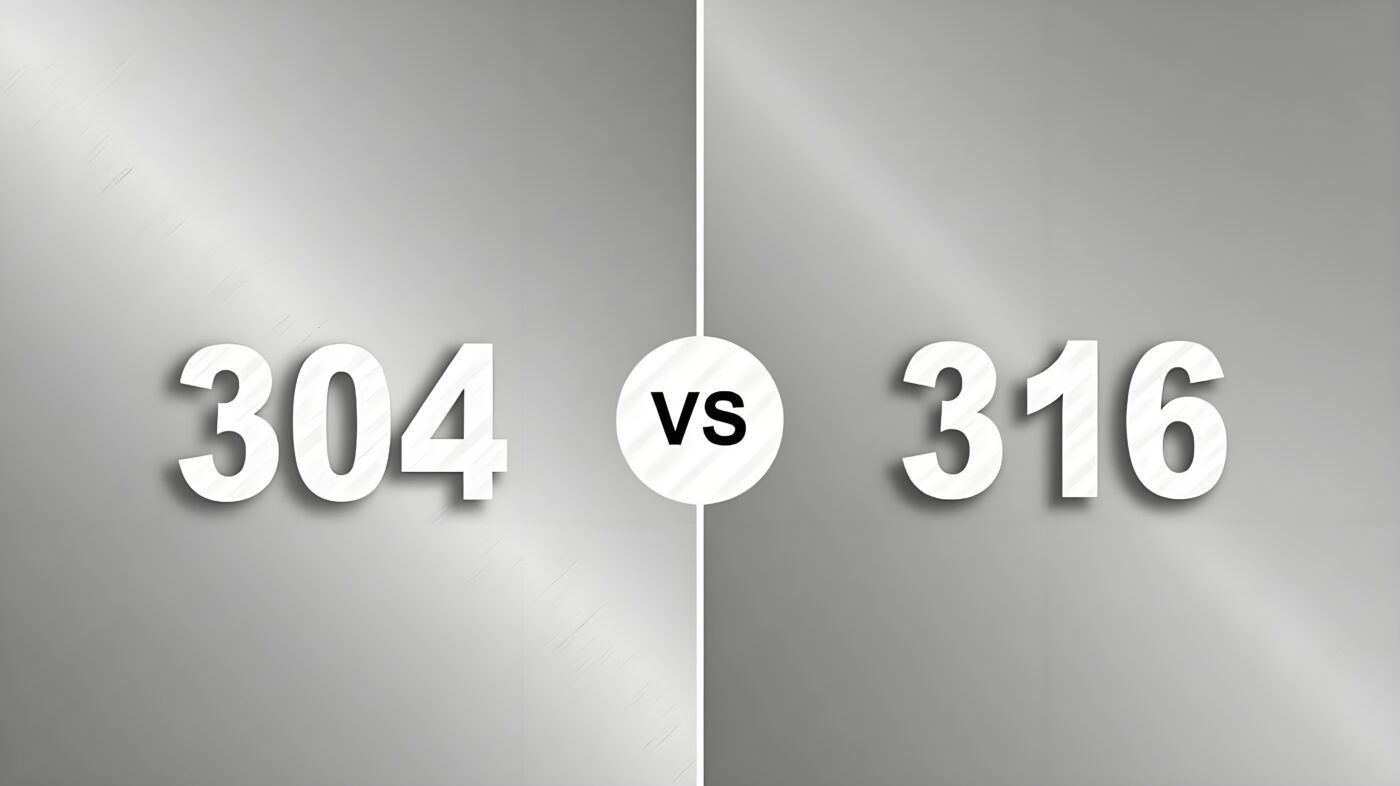
Stainless steel is a versatile material that finds its way into countless applications across industries. Among the many types, 304 and 316 stainless steel are two of the most widely used. They are both austenitic stainless steels that have different capabilities in rapid prototyping processes such as sheet metal fabrication and CNC machining. Understanding the scientific properties of these materials and how to choose between them based on your specific application needs can significantly affect the performance and longevity of your products.
In this article, we will dive deep into the properties of 304 and 316 stainless steel, exploring their strengths, limitations, and best-use scenarios. Additionally, we’ll walk through a practical case study—comparing the performance of insulated cups made from these two types of stainless steel, helping you understand how material selection impacts the final product.
1. Understanding 304 Stainless Steel
304 stainless steel is one of the most commonly ordered stainless steel grades due to its performance and properties, making it a key material across many industries. Its excellent corrosion resistance allows it to perform both functionally and aesthetically in a variety of environments. Additionally, its machinability and weldability make it a top choice for CNC machining and sheet metal fabrication. Many prefer 304 stainless steel for its aesthetic appeal when used in components for high-rise buildings and skyscrapers.
Chemical Composition
304 stainless steel is primarily composed of 18% chromium and 8% nickel, which gives it excellent corrosion resistance, making it ideal for environments exposed to humidity or certain corrosive substances. The high chromium content forms a thin oxide layer on the surface of the material, protecting it from rust.
Properties
- Corrosion Resistance: Good in most normal environments but can be susceptible to chloride-induced corrosion (e.g., saltwater environments).
- Strength: High tensile strength, making it durable for most general-use products.
- Temperature Resistance: Can withstand temperatures up to 870°C.
- Cost: Economical and widely available, making it a go-to for many industrial and consumer applications.
Applications
304 stainless steel is commonly found in:
- Architectural Decoration: With its smooth surface and excellent corrosion resistance, 304 stainless steel is widely used in both interior and exterior designs, such as stair railings, wall claddings, and elevator interiors.
- Food Processing Industry: Due to its outstanding corrosion resistance and hygiene properties, 304 stainless steel is commonly used in food processing equipment, kitchenware, and utensils.
- Medical Instruments: Thanks to its superior biocompatibility and resistance to corrosion, 304 stainless steel is extensively utilized in the manufacturing of medical devices, surgical tools, and implants.
- Mechanical Manufacturing: 304 stainless steel’s excellent strength and corrosion resistance make it a preferred material for various mechanical parts, bearings, and valves.
- Petrochemical, Chemical, and Marine Engineering: Its ability to withstand high temperatures, pressure, and corrosive media allows 304 stainless steel to be used in petrochemical, chemical equipment, and marine engineering.
- Automotive and Rail Industry: The corrosion resistance and strength of 304 stainless steel make it a key material in the automotive and rail industries, used in exhaust systems, doors, roofs, and more.
2. Understanding 316 Stainless Steel
Chemical Composition
316 stainless steel takes things a step further by adding molybdenum (about 2-3%), in addition to the 16% chromium and 10% nickel. This addition significantly boosts its corrosion resistance, particularly in chloride-rich environments like marine conditions or areas where chemicals are involved.
Properties
- Corrosion Resistance: Superior to 304, especially in chloride environments. It is highly resistant to pitting and crevice corrosion.
- Strength: Similar to 304 but with added durability in aggressive environments.
- Temperature Resistance: Can also handle high temperatures up to 800-850°C.
- Cost: More expensive than 304(about 60%-80%)due to the added molybdenum, but worth it for specific use cases.
Applications
316 stainless steel is commonly found in:
- Chemical Industry: 316 stainless steel is highly resistant to a wide range of chemicals, making it a popular choice for manufacturing storage tanks, pipelines, and valves in the chemical industry.
- Food Processing Industry: As a commonly used material in the food industry, 316 stainless steel is found in containers, processing equipment, and piping due to its excellent corrosion resistance.
- Medical Instruments: With its resistance to corrosion, high strength, and ability to withstand high temperatures, 316 stainless steel is frequently used in medical devices, surgical tools, and implants.
- Shipbuilding: Thanks to its exceptional corrosion resistance in seawater, 316 stainless steel is widely applied in shipbuilding and marine engineering.
- Construction Industry: Known for its high strength, aesthetic appeal, and corrosion resistance, 316 stainless steel is extensively used in architectural decorations, building components, and indoor furniture.
- Cosmetic Packaging: 316 stainless steel is used to craft durable and aesthetically pleasing cosmetic containers, powder cases, and lipstick tubes, meeting consumer demands for both beauty and quality.
3. Case Study: Performance of Insulated Cups Made from 304 vs. 316 Stainless Steel
Let’s explore how both 304 and 316 stainless steel perform in a real-world application: insulated cups.
In the construction of thermal insulation cups, there are multiple layers designed to minimize heat transfer. The inner layer typically features a vacuum, which prevents heat conduction. Additionally, a silver coating is often applied to block heat radiation. Some lids include cork stoppers to further reduce heat transfer.
Comparing 304 and 316 Stainless Steel in Thermal Insulation Cups:
- 304 Stainless Steel:
- A versatile stainless steel widely used in various industries.
- It offers good high-temperature resistance, with a typical upper limit of about 650°C.
- Its excellent corrosion resistance and intergranular corrosion protection make it a popular choice for many applications.
- 316 Stainless Steel:
- Contains 18% chromium, 12% nickel, and 2.5% molybdenum (Mo).
- The addition of molybdenum gives 316 superior resistance to corrosion, atmospheric wear, and higher strength in extreme conditions.
- It also has excellent work hardening properties and is non-magnetic.
In summary, both 304 and 316 stainless steels have their respective advantages. For applications like thermal insulation cups, 304 stainless steel is more than sufficient. However, for industries such as medical or chemical fields, or for use in extreme environments, 316 stainless steel is undoubtedly the better choice.
Regardless of which stainless steel you choose, the key is to make a well-informed decision based on actual needs, rather than being swayed by marketing tactics. This is the only way to ensure you’re not overpaying and that you’re getting the right, high-quality stainless steel product tailored to your requirements. (Working with Leanplans, we have your back! )
Conclusion
Both 304 and 316 stainless steel have their strengths, and understanding these differences is crucial to making the right choice for your project. For applications where cost is a concern and corrosion resistance is moderate, 304 stainless steel delivers excellent performance. However, for more demanding environments, 316 stainless steel is the go-to solution, providing unparalleled protection against corrosion and wear.
At Leanplans, we provide expert guidance on material selection for your custom parts, helping you strike the right balance between performance and cost. Whether you’re developing consumer goods, industrial parts, or medical equipment, we ensure that you get the most out of your material investment.
Get a Free Material Analysis for Your Projects!
Leave your contact details, or directly visit our online quoting platform to experience the future of material selection and production. Get expert material evaluations, tailored DFM analysis, cost-effective quotation and fast 24-hour production turnaround.
- Free Quote: Upload your designs, and our AI-powered engine will generate a cost-effective quote in 5 seconds.
- Talk to an Expert: Connect with one of our engineers via WhatsApp for immediate assistance.