As Machined Services
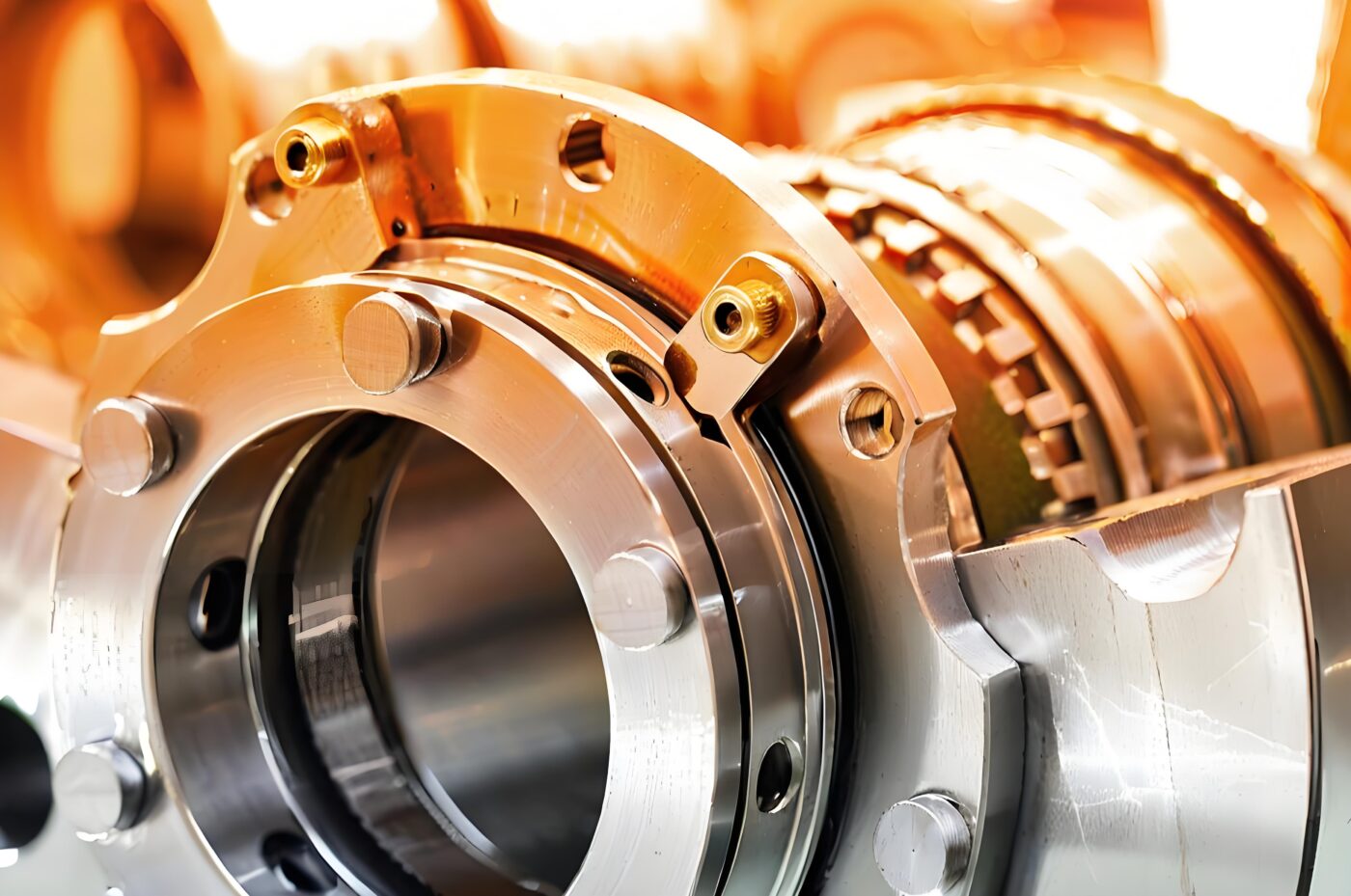
Welcome to CNC machining, the finish of a part plays a critical role in its performance and appearance. Among the various surface finishes available, the As Machined finish stands out for its practicality and cost-effectiveness.
This finish reflects the part’s raw state immediately after machining, retaining visible tool marks. While it offers some specific advantages, especially in prototyping and structural applications, understanding when to use or avoid this finish is essential for achieving the best results in different manufacturing scenarios.
What is As Machined surface finish?
The As Machined surface finish is the natural result of CNC machining, where the part retains visible tool marks without further polishing or treatment. This finish is highly practical for prototyping and structural parts since it preserves mechanical properties and reduces costs by skipping additional surface treatment steps.
The rough surface is also beneficial for adhesive bonding and powder coating, providing better adhesion. However, As Machined finishes are not ideal for aesthetically critical parts, low-friction applications, or industries requiring ultra-smooth surfaces, such as aerospace, medical, and food equipment. In these cases, smoother finishes are needed to meet performance and regulatory standards.
Our quality-driven As Machined services deliver parts with a surface finish featuring a roughness of Ra 3.2μm and Ra 1.6μm, all achieved without the need for additional finishing processes. This approach ensures that you receive high-quality components efficiently, maintaining both performance and cost-effectiveness.
Finish ★ ★
Tolerances ★ ★ ★ ★ ★
Protection ★
Cost ★
Suitable ★ ★ ★ ★ ★
Our quality-driven As Machined services deliver parts with a surface finish featuring a roughness of Ra 3.2μm and Ra 1.6μm (0.8μm/0.4μm depending on the requirements of the application), all achieved without the need for additional finishing processes. This approach ensures that you receive high-quality components efficiently, maintaining both performance and cost-effectiveness.
Design Considerations
As parts are produced, they may undergo various processes to improve their surface finish, such as grinding and polishing. However, some parts can be sold with an As Machined surface finish, meaning no additional treatments have been applied. This option is advantageous for cost savings and allows engineers to utilize unaltered parts in critical applications where material properties remain unaffected by further processing.
Despite its benefits, an As Machined surface finish requires careful consideration of potential oxidation effects. Unlike materials like plastic and stainless steel, pure metals such as copper and steel are particularly susceptible to oxidation, leading to rust and patina. This oxidation can negatively impact not only the appearance of the part but also its mechanical and electrical properties—affecting conductivity and increasing surface resistance.
The oxidation process is expedited by moisture and air, necessitating that engineers evaluate the operating environment and storage conditions. For instance, steel parts intended for outdoor storage should be coated with a rust inhibitor to mitigate early oxidation.
Internal surfaces of metal components can also be affected, as oxidation may accumulate within the part, leading to fluid flow blockages and reduced mechanical strength. Oxidized steel, for example, can become more brittle and less robust.
Consequently, engineers must meticulously assess the intended environment and application of parts with an As Machined surface finish. Proper documentation of the finish is essential to inform engineers of its implications. Additionally, consideration should be given to the possibility of burrs and sharp edges on metal parts, particularly those made from softer materials like aluminum. Such edges can lead to mechanical failure or injury.
Another challenge associated with As Machined metal parts is the presence of swarf, which may linger in drilled holes. This residue can disrupt subsequent manufacturing processes and the part’s final application; swarf in an engine block, for instance, could result in oil leaks from passages.
Practical Uses of As Machined Finish
For prototypes, using an As Machined finish allows for faster iteration at a lower cost. This finish doesn’t require extra processing, so engineers can quickly test and refine designs without delays. Structural parts also benefit from the finish as their primary function—ensuring stability and strength—doesn’t rely on surface smoothness. Similarly, parts destined for powder coating or adhesive bonding see an advantage since the rough surface enhances the adherence of coatings or adhesives.
Limitations of As Machined Finish
While this surface finish can save time and money, it’s not suitable for applications demanding high precision or smooth surfaces. Aesthetic components or those used in environments where friction needs to be minimized—such as in bearings, seals, and rotating parts—require smoother finishes. Industries like aerospace and automotive, which prioritize tight tolerances and refined surface treatments, also typically avoid As Machined finishes.
Furthermore, sectors such as medical or food processing demand finishes that meet strict cleanliness and safety standards. The rougher surface left by As Machined processing may harbor contaminants, making it unsuitable for applications involving contact with food or pharmaceuticals. Optical devices and electronic enclosures, which often need a highly polished or flawless surface, also don’t benefit from this type of finish.
Why Choose Leanplans Finishing Services?
Manufacturing a part often involves various challenges, from design miscommunications to machining inaccuracies that can lead to defects. Poor material selection can also result in parts that fail under stress. Surface finishes play a crucial role in both aesthetics and performance, but not all materials are suited for every finish, and improper application can yield negative results.
While understanding the interplay between materials and finishes is essential, this expertise is not always accessible to engineers. Leanplans steps in with years of manufacturing experience, providing valuable guidance to help customers achieve optimal results for their projects.
Our reliability and proven track record speak to our capabilities as a manufacturer. With over 1.5 million parts produced, we possess the expertise and resources to meet any manufacturing demand, from rapid prototypes to large-scale production runs. Our consistent delivery of high-quality parts fosters trust among our customers, particularly for critical and complex components, making Leanplans a preferred partner for you!
FAQs:
- What Factors Affect the Quality of a Machined Surface?
The quality of an as-machined surface finish is influenced by several key factors, including the quality of the machine tool, the rigidity of the setup, and the cutting parameters such as feed rates and cutting speeds. Additionally, the skills of the operator play a crucial role. Material sourcing also significantly impacts surface quality. For personalized assistance in selecting the appropriate material, please reach out to your sales engineer or contact us at sales@lepumake.com. - Why Do Turned Parts Appear Smoother Than Milled Parts When Using the Same Material?
Turned parts generally have a smoother surface finish than milled parts due to the continuous contact between the cutting tool and the workpiece during the turning process. This consistent cutting action is achieved using single-point cutting tools, which produce a uniform surface. In contrast, milling uses multi-point cutting tools with multiple edges, leading to surface variations from intermittent contact. Additionally, the precise control over feed rate and depth of cut in turning contributes to a finer finish compared to the rougher surfaces often produced in milling. - What Are the Common Applications for As-Machined Finishes?
As-machined finishes are commonly used in applications where aesthetics are less critical but performance is essential. These finishes are ideal for structural components, prototype parts, and applications involving adhesive bonding or powder coating. The cost-effectiveness of as-machined finishes makes them suitable for large production runs and parts that will undergo further processing. However, they are generally not recommended for high-precision applications or components that require stringent surface finish specifications.
Get a Free Quote!
Leave your contact details, or directly visit our online quoting platform to experience the future of material selection and production. Get expert material evaluations, tailored DFM analysis, and fast 24-hour production turnaround.
- Free Quote: Upload your designs, and our AI-powered engine will generate a custom quote in seconds.
- Talk to an Expert: Connect with one of our engineers via WhatsApp for immediate assistance.