Injection Molding Design Guide
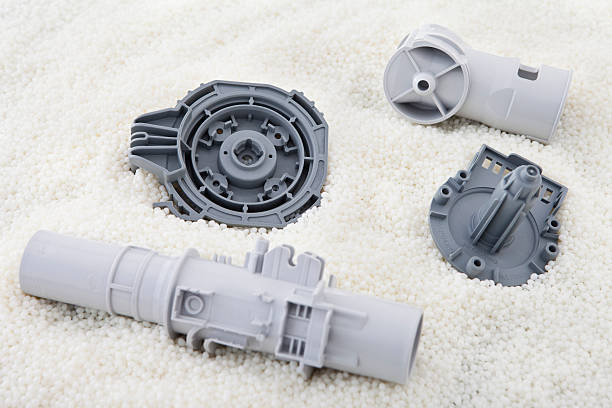
Injection molding is one of the most versatile and widely used manufacturing processes in modern production, offering a reliable way to produce large quantities of plastic parts with precision. The process involves melting plastic materials and injecting them into a custom-made mold, which gives the material its final shape. What makes injection molding particularly popular is its ability to replicate complex designs while maintaining cost efficiency, making it ideal for industries like consumer electronics, automotive, medical devices, and packaging.
1. What is Injection Molding?
Injection molding is a highly efficient process for producing plastic parts, and it relies on a specialized tool known as the injection mold. This mold consists of two primary components: the core and the cavity. When the two halves of the mold close together, molten plastic is injected into the space between them, taking the shape of the part being produced.
Once the plastic has cooled and solidified, the mold opens, and the finished part is ejected. Depending on the complexity of the mold and the volume of parts required, this cycle can be repeated tens, hundreds, or even thousands of times, making it ideal for mass production.
While this provides a basic understanding of the injection molding process, the true value lies in mastering the design elements involved. Injection molding design is a multi-step process that involves careful planning and refinement at every stage:
- Designing Your Part: The initial phase requires creating a detailed design that balances functionality and manufacturability.
- Uploading Your Design and Getting DFM Feedback: Once the design is complete, uploading it for analysis allows for valuable Design for Manufacturing (DFM) feedback, which ensures that the design is optimized for efficient and cost-effective production.
- Reviewing Part Samples: Finally, after production, reviewing part samples is crucial to ensure that the product meets all quality and performance expectations.
A Brief History
The history of injection molding dates back to the late 19th century, evolving from a simple method used to produce combs and buttons into the high-tech, highly automated process we know today. Over the years, advancements in plastic materials, along with the introduction of more sophisticated machinery, have transformed injection molding into a cornerstone of modern manufacturing. By the mid-20th century, this technique was firmly established in various industries, with automation helping to boost production rates and reduce costs.
2. How Injection Molding Works
At its core, the injection molding process is straightforward. Plastic pellets are first heated in a barrel, where they melt and become pliable. This molten plastic is then forced into a mold cavity at high pressure, filling every nook and cranny of the design. Once inside, the material cools and solidifies, after which the mold opens, and the newly formed part is ejected. This process, while simple in principle, can produce highly detailed parts with tight tolerances, which is why it’s so prevalent in industries requiring precision.
- Melting & Plasticizing: Plastic pellets are heated and melted inside a barrel with a rotating screw.
- Injection: The molten plastic is injected into the mold cavity under high pressure.
- Cooling & Solidifying: The plastic cools and solidifies inside the mold, taking the shape of the cavity.
- Ejection: The mold opens, and the finished part is ejected.
3. Key Considerations in Injection Molding Design
Design Factors
- Draft Angle:Draft angles are essential in injection-molded parts to ensure they can be easily removed from the mold without causing damage. The required draft angle depends on several factors, including wall thickness, material shrinkage, and any post-production finishing requirements.
A general guideline is to increase the draft angle by 1 degree for every inch of depth, though a safe starting point for most components is typically between 1.5 to 2 degrees. If the surface requires a heavy texture, the draft angle may need to increase to as much as 5 degrees per inch of depth. Insufficient draft can lead to issues like drag marks, which affect both the aesthetics and functionality of the part.
Draft angles can be added using CAD software, but it’s best to incorporate them in the final stages of the design process to avoid adding unnecessary complexity during earlier development stages.
- Uniform Wall Thickness:Wall thickness plays a crucial role in shaping the performance, appearance, and cost of an injection-molded component. Determining the optimal wall thickness is essential and should be based on the part’s functional requirements, taking into account factors such as allowable stress and the desired lifespan of the part.As a general guideline, maintaining uniform wall thickness throughout the component is recommended. Typically, an ideal range falls between 1.2mm and 3mm. Walls that are too thin may require higher injection pressures, leading to potential issues like air traps. Conversely, excessively thick walls can result in increased costs due to longer cooling times and higher material consumption.If variations in wall thickness are necessary, it’s important to implement smooth transitions between sections. This can be done by adding chamfers to sloped edges or corners. Similarly, using fillets to round off edges will promote even flow of the molten plastic during injection and ensure uniform cooling across the part, reducing the risk of defects.
- Ribs:
Add ribs to reinforce structural integrity without increasing material use. Ribs are essential for reinforcing part walls, particularly where two walls meet at a 90-degree angle. They enhance the overall structural integrity of the part, improving its strength and load-bearing capacity without adding unnecessary bulk.
Similarly, bosses serve a critical role in part design by providing raised areas that are used for fastening or aligning components. They are commonly found around screw holes and slots, adding strength to these areas and ensuring the part remains robust under mechanical stress.
- Shrinkage:Shrinkage is a key consideration in injection molding, as each material contracts at a specific rate as it cools. If not accounted for, shrinkage can lead to undersized or warped parts. Different materials, like polypropylene and ABS, have varying shrinkage rates, so it’s essential to adjust mold dimensions accordingly.Factors such as wall thickness, cooling time, and mold temperature also affect shrinkage. Thicker sections tend to shrink more than thinner ones, so maintaining uniform wall thickness can help reduce issues. Proper design and cooling management are crucial to ensuring parts meet specifications and avoid defects.
Mold Design Considerations
- Cavity Count: The cavity count of a mold refers to the number of identical parts that can be produced in a single injection cycle. Utilizing multi-cavity molds can significantly enhance production efficiency, particularly when dealing with high-volume demands. By increasing the number of cavities, manufacturers can produce multiple parts simultaneously, thereby reducing cycle times and lowering the cost per part. This approach not only improves throughput but also optimizes the use of materials and energy, making the manufacturing process more sustainable. However, careful consideration must be given to the design and layout of the cavities to ensure uniform filling and cooling, as well as to avoid potential issues such as imbalance in flow rates or differences in cooling times.
- Gate Design: Gate design is a critical aspect of injection molding that impacts both the quality of the final product and the efficiency of the production process. Proper placement of gates minimizes visible marks on the finished parts while ensuring even distribution of molten plastic throughout the mold. Common gate types, such as edge gates and pinpoint gates, each serve different purposes and can be selected based on the specific requirements of the part design. For instance, edge gates are typically used for larger parts, providing a larger flow path for the plastic, while pinpoint gates are better suited for smaller, more intricate components. An optimal gate design not only improves aesthetic quality by reducing gate marks but also enhances the mechanical properties of the part by ensuring consistent fill and pressure during molding.
- Cooling Channels:
4. Material Selection for Injection Molding
Injection molding materials encompass a wide range of plastics, from common polymers to specialized blends. With hundreds of plastic resins available, each offers unique end-use properties and processing requirements, including variations like glass or carbon fiber reinforcements.
Resin | Characteristics |
---|---|
Acetal (POM) | Known for its rigidity and thermal stability, Acetal has low water absorption and good chemical resistance, making it ideal for precision components. |
Acrylic (PMMA) | This lightweight material is shatter-resistant, optically clear, and highly resistant to UV and weather, often used in transparent applications. |
Acrylonitrile Butadiene Styrene (ABS) | Offers robust impact resistance even at low temperatures, making it suitable for durable applications. |
Nylon (PA) | Celebrated for toughness, heat resistance, and excellent abrasion resistance, Nylon is ideal for demanding environments. |
Polybutylene Terephthalate (PBT) | Resistant to creep, PBT is great for components with thin cross-sections requiring stability under load. |
Polycarbonate (PC) | Strong and lightweight, polycarbonate is naturally transparent and stable across a broad temperature range, suitable for various uses. |
Polyether Ether Ketone (PEEK) | Known for excellent mechanical properties and resistance to chemicals and thermal degradation, PEEK is ideal for high-performance applications. |
Polyetherimide (PEI) | Combines stiffness and low flammability, making PEI suitable for sensitive environments. |
Polyethylene (PE) | Used for indoor applications, polyethylene is chemically resistant and available in high-density and low-density variants. |
Polyphenylsulfone (PPSU) | Features high toughness and resistance to heat and chemicals, suitable for challenging environments. |
Polypropylene (PP) | Offers good chemical resistance and durability, stable even in moist conditions. |
Polystyrene (PS) | Lightweight and cost-effective, polystyrene resists moisture and bacterial growth, common in various applications. |
Thermoplastic Elastomer (TPE) | Exhibits properties of both plastic and rubber, providing flexibility and resilience. |
Thermoplastic Polyurethane (TPU) | Characterized by rubber-like elasticity and strong load-bearing capabilities, TPU is ideal for flexible and robust applications. |
5. Limitations of injection molding
- High Start-Up Costs for Tooling: One of the primary economic challenges associated with injection molding is the significant cost of tooling. Each unique part geometry requires a custom mold, leading to substantial start-up expenses. The design and manufacturing of these molds can range from $5,000 to $100,000, depending on complexity and specifications.As a result, injection molding becomes economically feasible primarily for production runs exceeding 500 units. This high initial investment necessitates careful planning and consideration for manufacturers looking to utilize this efficient production method.
- Longer Lead Times Compared to Other Technologies: Injection molding typically has a longer turnaround time than many other manufacturing methods, ranging from 6 to 10 weeks. This timeframes includes 4 to 6 weeks dedicated to mold fabrication, followed by an additional 2 to 4 weeks for production and shipping. If design modifications are necessary—which is a common occurrence—the overall lead time can increase significantly.In contrast, parts produced using desktop 3D printing can often be ready for delivery within a single day, while industrial 3D printing systems usually have a lead time of 3 to 5 days. CNC machining offers a similarly quick turnaround, with parts typically delivered in 10 days, and in some cases, as fast as 5 days. This disparity in lead times makes injection molding less suitable for projects requiring rapid prototyping or quick production cycles.
6. Common Applications of Injection Molding
Injection molding is used across multiple industries, including:
- Consumer Electronics:
In the realm of consumer electronics, injection molding plays a crucial role in the production of essential components. This includes items like phone cases, which are designed to be durable yet lightweight, ensuring both protection and usability. Keyboards benefit from injection molding by allowing for precise, molded keycaps that enhance user experience. Additionally, connectors, switches, and housings for electronic devices are often created through this process, enabling manufacturers to achieve intricate designs and high levels of detail that are both functional and aesthetically pleasing.
- Automotive:
The automotive industry heavily relies on injection molding for manufacturing various components that contribute to both the performance and safety of vehicles. Common applications include dashboard components, which are often molded to create complex shapes and textures that improve the vehicle’s interior design. Light housings, essential for vehicle visibility and safety, are also produced using injection molding, ensuring they are robust enough to withstand harsh conditions while providing an appealing appearance. Other applications in this sector include clips, fasteners, and various enclosures that play critical roles in the assembly and operation of vehicles. - Medical Devices:
In the medical field, injection molding is indispensable for creating precision components that meet stringent regulatory standards. Common applications include syringes, which require high levels of accuracy and safety to ensure proper dosage and patient care. Surgical tools, often made from specialized plastics to enhance sterility and ease of use, are also produced through this process. Additionally, components for diagnostic equipment, such as casings and connectors, benefit from the consistency and reliability offered by injection molding, making it a preferred choice for manufacturers in the healthcare sector.
- Packaging:
Another significant application of injection molding is in the packaging industry. This process is used to create durable and lightweight containers, caps, and closures that protect products while providing convenience for consumers. The ability to produce intricate designs allows for innovative packaging solutions that enhance user experience and brand recognition.
Get a Free Quote!
Leave your contact details, or directly visit our online quoting platform to experience the future of material selection and production. Get expert material evaluations, tailored DFM analysis, and fast 24-hour production turnaround.
- Free Quote: Upload your designs, and our AI-powered engine will generate a custom quote in seconds.
- Talk to an Expert: Connect with one of our engineers via WhatsApp for immediate assistance.