Beyond the Surface: The Unseen Power of Aluminum Extrusion in Innovation
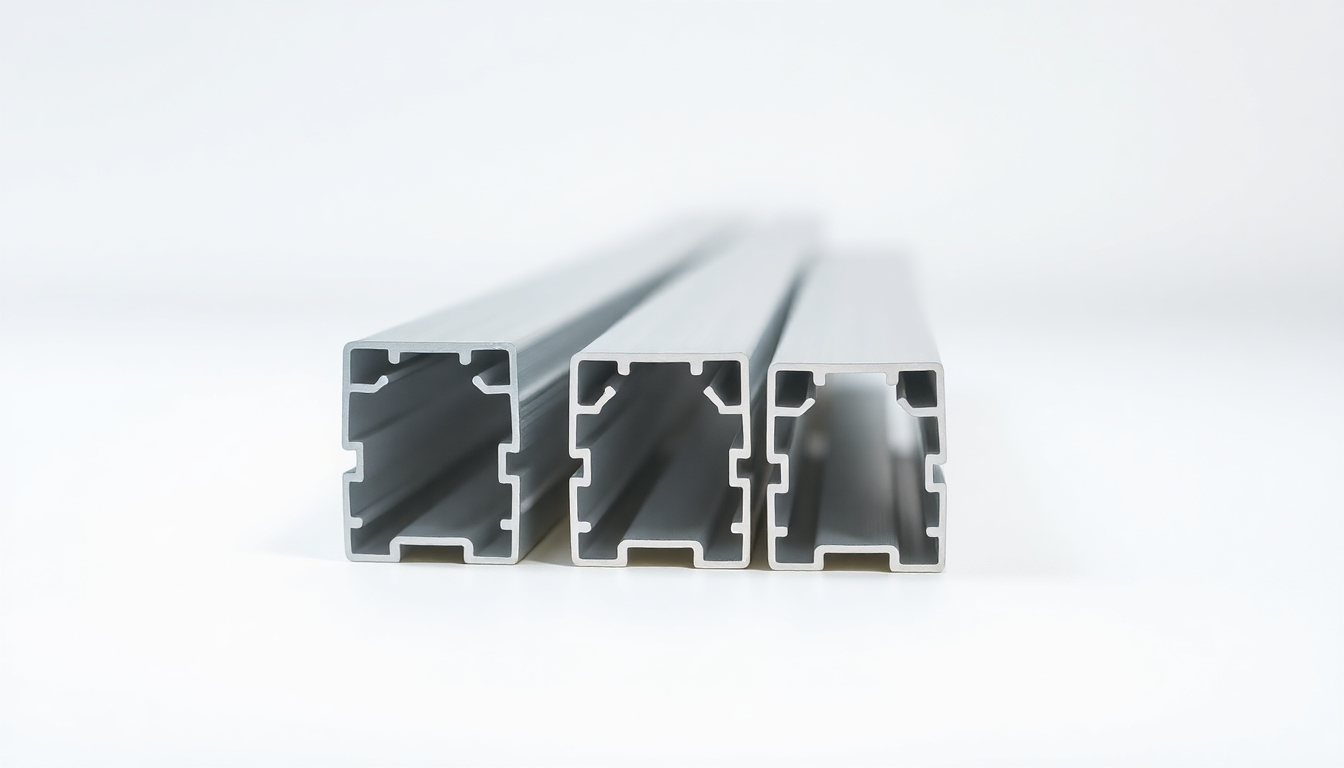
1. Aluminum Extrusion Process Explanation
The aluminum extrusion process involves applying a substantial amount of pressure to aluminum billets placed in a die cavity or extrusion cylinder. This pressure forces the aluminum material to undergo directed plastic deformation, which then exits through the die opening to form the desired cross-sectional shape and mechanical properties required for the final part or semi-finished product.
The process is analogous to squeezing toothpaste from a tube. The aluminum billet is pushed through a die to shape it into profiles like bars, pipes, or other specialized components.
In the diagram below, we can see an aluminum alloy automotive bumper beam along with its extrusion die. Under pressure, the aluminum ingot is split into several metal flows, which enter the welding chamber through distribution holes. In this chamber, the aluminum is re-welded under high temperature, pressure, and vacuum, before being forced out through the gap between the die core and die opening, forming hollow or solid profiles. If bending is required, additional tools are added in the subsequent equipment.
2. Extrusion Dies Section
What is an Extrusion Die?
An extrusion die is essentially a thick steel disk containing one or more openings designed to form the desired profile of the extruded material. These dies are typically made from H-13 tool steel, which is heat-treated to withstand the high pressure and temperature of the aluminum as it passes through.
Although aluminum is often considered a relatively soft metal, significant pressure is required to push solid aluminum billets (also known as aluminum ingots) through these thin, porous dies to create the desired shapes.
Definition of Aluminum Billets:
An aluminum billet is a semi-finished product typically created by casting molten aluminum. These billets are then processed further in extrusion operations.
Types of Extrusion Dies:
Extrusion dies can be classified into three categories based on the cross-sectional shape of the aluminum extrusion:
- Solid Dies: These are used for creating solid profiles with no hollow sections.
- Semi-Hollow Dies: These are used for producing profiles with partial hollows or cavities.
- Hollow Dies: These are used for making complex hollow profiles and are generally more expensive due to their intricate design and higher wear.
The hollow die is the most complex and prone to wear and fracture, making it the most costly to manufacture.
Die Life and Durability:
The die life is primarily affected by heat buildup and uneven pressure distribution caused by factors like thin walls, uneven wall thickness, and protruding features in the extruded profile. Experienced die engineers can design dies that control heat distribution and pressure to extend the life of the die, but eventually, all dies must be replaced.
When designing aluminum extrusion parts, structural engineers should understand which design features significantly affect die manufacturing costs. In cases where it’s feasible, modifying the design of the aluminum extrusion profile, setting appropriate tolerances, or selecting suitable aluminum alloy materials can help reduce die costs.
3. Advantages of the Aluminum Extrusion Process
- Durability and Corrosion Resistance
One of aluminum’s most significant advantages is its resistance to corrosion and weathering. Aluminum naturally forms a thin oxide film on its surface, which protects it from corrosion. This makes it highly durable even in harsh environmental conditions. Additionally, anodizing aluminum further enhances its corrosion resistance and surface quality.
For instance, a 25-micron anodizing layer can improve both the corrosion resistance and surface finish of the material, making it ideal for outdoor applications without requiring additional maintenance.
- Lightweight and Strong
Aluminum is approximately 33% lighter than steel, while retaining most of its strength. The tensile strength of most aluminum alloys ranges from 70-700 MPa, with a density that is roughly one-third that of steel.
This makes aluminum an excellent choice for structural components in industries like construction and automotive. The automotive industry, in particular, is increasingly adopting aluminum alloys to reduce vehicle weight and improve fuel efficiency.
- Excellent Thermal Conductivity
Aluminums’ thermal conductivity is similar to copper, but it is much lighter. Aluminum is an excellent heat conductor, and extrusion profiles can be designed to maximize heat transfer surface area, such as in computer CPU heat sinks. - Aesthetic Versatility
Aluminum extrusions can be painted, anodized, electroplated, or polished, providing a wide range of aesthetic options. Engineers can customize the appearance of aluminum extrusions to meet specific design requirements. - Wide Application Range
Nearly any cross-sectional shape can be created through the aluminum extrusion process, offering broad design flexibility. Engineers can design a variety of profiles to meet the demands of different applications. - Ease of Secondary Processing
Aluminum extrusions are easy to form, cut, drill, machine, punch, bend, and weld to meet specific needs. This makes aluminum extrusions versatile and adaptable for a wide range of applications. - Cost-Effective Tooling and Quick Turnaround
Aluminum extrusion dies are relatively simple, with a short processing cycle and low manufacturing costs. This makes aluminum extrusion an economical option for producing both small and large volumes of parts. - Impact Resistance and Energy Absorption
Aluminum extrusions can absorb impact energy and deform under load without losing their strength or flexibility. This makes them ideal for applications where shock absorption is crucial, such as in transportation and building structures.
- Environmentally Friendly
Aluminum is a sustainable material, and it is highly recyclable. The recycling rate of aluminum is nearly 90% globally, which significantly reduces its environmental footprint.
4. Applications of Aluminum Extrusion
Aluminum is often regarded as the metal of the future due to its environmental benefits, lightweight nature, inherent corrosion resistance, high strength, and excellent thermal and electrical conductivity.
According to the Aluminum Association (AA) and the Aluminum Extruders Council (AEC), the use of aluminum extrusions in North America has grown for six consecutive years, accounting for nearly a quarter (22%) of the total aluminum market in the region.
Although the construction industry remains the largest user of aluminum extrusions, more and more industries are adopting aluminum extrusions due to their nearly unlimited design possibilities.
Below are seven key industries where aluminum extrusion is at the core of innovation:
- Aerospace and Aviation
Aluminum has been a critical component in the aerospace industry since the beginning. The Wright brothers’ first aircraft used aluminum engine parts to reduce weight. Today, aluminum accounts for 75-80% of modern aircraft due to its lightweight yet durable properties. Many spacecraft components are also made from aluminum due to its high strength-to-weight ratio. - Transportation Industry
In the transportation sector, where strength-to-weight ratio is crucial, aluminum extrusions are ideal for components like engine blocks, transmission housings, panels, chassis, and body frames in cars, trucks, trains, and ships. The transportation industry is the second-largest consumer of aluminum extrusions, and its demand is continuously growing. From Ford to Audi to Mercedes-Benz, automotive engineers are constantly seeking ways to replace steel parts with aluminum to improve fuel efficiency and performance. Electric vehicles (EVs) also extensively use aluminum for lightweighting.
- Building Products Industry
Unlike steel, aluminum can be extruded into complex shapes and manufactured to meet strict architectural specifications, making it a popular choice for building materials. From windows and doors to balconies and roofs, architects are increasingly turning to aluminum for green, sustainable buildings that stand the test of time. - Consumer Goods Industry
Since aluminum extrusions were first introduced in appliances like washing machines and dryers, they have revolutionized the market. Today, many everyday items, including fitness equipment and furniture, are made using aluminum extrusions.
- Electronics Industry
Aluminum extrusions are used in various electronic devices due to their unique thermal and electrical conductivity properties. Custom aluminum profiles are commonly used for motor housings, heat sinks, and internal frames in products like laptops, smartphones (e.g., Apple iPhones), and flat-screen televisions. - Lighting Industry
Due to aluminum’s excellent thermal conductivity, engineers can design complete extruded LED lighting fixtures that provide optimal heat dissipation, ensuring maximum thermal efficiency. Moreover, the relatively low cost of extrusion dies, coupled with the ease of cutting, shaping, and anodizing or painting aluminum, makes it a perfect fit for efficient lighting solutions. - Solar Industry
Aluminum extrusions are ideal for solar panel mounting systems, providing the strength needed to withstand environmental factors like snow and wind, without adding excess weight. This makes aluminum extrusions a preferred choice for solar energy applications, including rooftop panels and Building-Integrated Photovoltaics (BIPV) systems.
Get a Free Quote!
Leave your contact details, or directly visit our online quoting platform to experience the future of material selection and production. Get expert material evaluations, tailored DFM analysis, and fast 24-hour production turnaround.
- Free Quote: Upload your designs, and our AI-powered engine will generate a custom quote in seconds.
- Talk to an Expert: Connect with one of our engineers via WhatsApp for immediate assistance.