Rapid Prototyping Manufacturing Guide
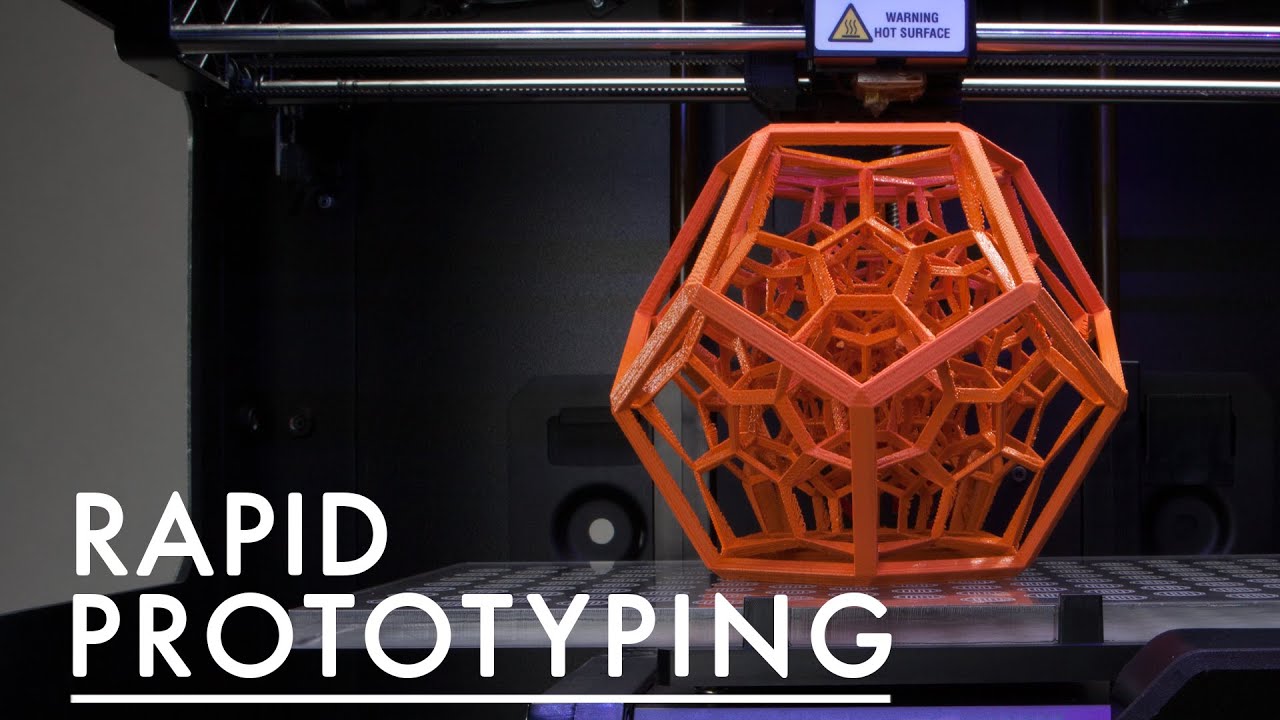
What is Rapid Prototyping?
Rapid prototyping refers to various processes used to produce complete parts, custom products, and low-volume items efficiently. Unlike traditional manufacturing methods—such as injection molding and forming—which often involve costly tools and extended timelines, rapid prototyping leverages software automation and modern technology to create both simple and complex products at a fraction of the cost and time.
Using tools like Leanplans’ 3D printers, teams can transform ideas into realistic proofs of concept and advance them to high-fidelity prototypes that closely resemble the final products. Moreover, 3D-printed prototypes are budget-friendly, enabling the production of numerous affordable prototypes with quick turnaround times.
Benefits and Advantages of Rapid Prototyping
Rapid prototyping is a highly efficient design and development method that comes with numerous advantages. First and foremost, it allows teams to quickly prototype and test their ideas, ensuring they’re on the right track before diving deeper into the manufacturing process. This is particularly crucial in the early stages of prototyping, where concepts are still evolving and being refined.
One of the main goals of rapid prototyping is to produce a functional prototype that closely resembles the envisioned final product. By utilizing technologies like 3D printing and additive manufacturing, teams can create high-fidelity prototypes that give stakeholders a tangible feel for what the finished product will look and function like. Moreover, rapid prototyping isn’t just about creating objects; it focuses on iterating and improving designs based on feedback, ensuring that the final product meets user needs and expectations.
It’s important to note that rapid prototyping is not intended to replace comprehensive product design or development processes. Instead, it offers product managers a chance to quickly generate and validate new ideas in a cost-effective way. By enabling teams to identify potential issues and gather feedback early on, rapid prototyping significantly reduces the risk of incurring costly revisions later in the process.
Types of Rapid Prototyping
Stereolithography (SLA) employs laser-cured photopolymer to construct parts layer by layer. This method achieves strengths ranging from 2,500 to 10,000 psi and typically features additive layers measuring between 0.002 and 0.006 inches. SLA is particularly effective for producing highly detailed prototypes and visual models, utilizing thermoplastic-like photopolymers.
- Pros:
- High Precision: Can produce extremely detailed prints, ideal for complex designs.
- Excellent Surface Finish: Results in visually appealing finished products.
- Cons:
- Limited Material Strength: Not suitable for high-load or high-temperature environments.
- Post-Processing Time Required: Usually needs support removal and post-curing.
Selective Laser Sintering (SLS) utilizes a laser to sinter powdered materials, resulting in parts with strengths from 5,300 to 11,300 psi. The additive layers in SLS are approximately 0.004 inches thick and commonly employ materials such as nylon and thermoplastic polyurethane (TPU). This process is ideal for creating functional prototypes that require durability and resilience.
- Pros:
- Material Diversity: Can use various powder materials suitable for many applications.
- High Strength: Suitable for load-bearing or functional parts.
- Cons:
- Higher Cost: Equipment and powder materials can be expensive.
- Longer Print Times: Complex parts may require significant printing time.
Direct Metal Laser Sintering (DMLS) is specifically designed for metal applications. By sintering metal powders with a laser, DMLS achieves impressive strengths ranging from 37,700 to 190,000 psi. The additive layers are notably fine, measuring between 0.0008 and 0.0012 inches. DMLS is perfect for producing complex and robust metal parts, utilizing materials such as stainless steel, titanium, and aluminum.
- Pros:
- High Strength: Ideal for manufacturing parts that require high strength.
- Complex Design Capability: Can create intricate geometries, especially for aerospace and medical applications.
- Cons:
- High Cost: Equipment and metal powder materials are quite expensive.
- Slower Production Speed: Compared to other additive manufacturing technologies, DMLS has lower production speeds.
Fused Deposition Modeling (FDM) works by extruding melted thermoplastic material through a nozzle. This technique produces parts with strengths between 5,200 and 9,800 psi, with additive layers ranging from 0.005 to 0.013 inches. FDM commonly uses materials like ABS and polycarbonate, making it suitable for both prototypes and functional parts, although the surface finish may not be as refined as that achieved by SLA or SLS.
- Pros:
- Economical Equipment: Widely available desktop printers are suitable for individuals and small businesses.
- Easy to Operate: Relatively simple to operate and maintain.
- Cons:
- Poor Surface Finish: Lower print precision and surface smoothness; suitable for functional prototypes rather than aesthetics.
- Limited Material Options: Fewer types of materials available.
Multi Jet Fusion (MJF) employs an inkjet array to selectively fuse nylon powder, yielding strengths around 6,960 psi. The typical layer thickness is approximately 0.0035 to 0.008 inches. MJF is particularly effective for creating intricate geometries with a good balance of strength and production speed.
- Pros:
- Fast Production: High production speed makes it suitable for large-scale manufacturing.
- Good Surface Finish: High-quality finished products, ideal for final products.
- Cons:
- High Equipment and Material Costs: Initial investment is significant.
- Strong Dependence on Materials: Performance differences in materials can impact the final product.
PolyJet (PJET) technology utilizes UV-cured photopolymers, achieving strengths between 7,200 and 8,750 psi with remarkably fine layers measuring 0.0006 to 0.0012 inches. This method is ideal for producing highly detailed parts with smooth surfaces and is often used in applications that require high aesthetic quality.
- Pros:
- Multi-Material Printing: Capable of printing various materials, enhancing design flexibility.
- Good Visual Appeal: Suitable for multi-color and complex structure prints.
- Cons:
- Slower Printing Speed: Compared to other technologies, it is slower.
- Limited Strength: Strength and durability are restricted.
Computer Numerically Controlled Machining (CNC) employs traditional machining techniques to create parts from solid blocks of material. The strength of CNC-produced parts varies widely, ranging from 3,000 to 20,000 psi. The resulting surface finish is typically smooth due to the subtractive machining process. CNC machining can accommodate a variety of commodity and engineering-grade thermoplastics and metals, making it a versatile option for numerous applications.
- Pros:
- High Precision: Can achieve extremely high precision, suitable for functional parts.
- High Material Strength: Suitable for manufacturing high-strength components.
- Cons:
- Higher Costs: Equipment and material costs are significant.
- Longer Machining Times: Complex designs can result in extended machining times.
The 4 Steps of Rapid Prototyping
Step 1: Generate the 3D Files
The initial step involves developing the 3D files for your product. Partnering with design firms that specialize in 3D file creation can be highly advantageous. Additionally, creating 2D designs is recommended, especially when precision tolerances are required. It’s essential to clearly define the project specifications, which will depend on how the components will be utilized and any technical constraints. Once the 3D files and specifications are finalized, they can be forwarded to a rapid prototyping company like LEADRP.
Step 2: Assess the Costs
In the next phase, a specialized prototyping firm will evaluate the quantity and technical characteristics of the components to determine the cost of the rapid prototyping project. This assessment primarily considers the materials, manufacturing processes, finishes, and geometries of the prototypes. During this costing phase, you can also validate that the parts will function correctly. If necessary, modifications can be made to the 3D files. An accurate quote requires a comprehensive 3D part drawing.
Step 3: Initiate Production
After all elements of the project have been reviewed and approved, production can commence. If the design is intricate, it’s wise to create parts or sample plates before proceeding with the complete rapid prototyping production process.
Step 4: Conduct Testing
Once production is completed, a critical testing phase is conducted to ensure that the parts meet the initial requirements set forth.
Essential Considerations:
- Prototype Geometries: Confirm that the design aligns with the established specifications.
- Physical and Mechanical Attributes: Ensure the materials will perform as expected under operational conditions.
- Aesthetic Features: Focus on the visual aspects, including color selection, adhering to Pantone and RAL standards.
- Measurements: Verify all dimensions, paying particular attention to critical diameters.
- Surface Finish Rendering: Confirm that the finish meets the desired standards.
Comparison of Rapid Prototyping Technologies
Stereolithography (SLA):
SLA offers high resolution (★★★★★) and exceptional accuracy, making it suitable for quick prototypes with a high-quality finish. With a build volume of up to 300 x 335 x 200 mm, SLA employs a variety of resins, including engineering-grade, dental, and medical (biocompatible) materials, allowing it to produce high-fidelity, functional prototypes that require smooth surfaces. It is a user-friendly (★★★★★) and versatile option for producing precise, detailed models.
Selective Laser Sintering (SLS):
SLS is optimal for complex geometries and high-performance engineering prototypes. It boasts high resolution (★★★★☆), accuracy (★★★★★), and surface quality (★★★★☆) and can work with engineering thermoplastics, particularly nylon and its composites. SLS systems can build up to 165 x 165 x 300 mm on benchtop industrial printers, with equipment pricing from $19,000 for benchtop models to traditional industrial printers above $100,000. Although not as easy to use as other options (★★★★☆), SLS excels in creating durable, intricate parts.
Fused Deposition Modeling (FDM):
FDM is known for its accessibility and affordability, making it suitable for basic proof-of-concept models and simple low-cost prototypes. Its build volume reaches up to 300 x 300 x 600 mm with desktop and benchtop 3D printers, and it typically uses thermoplastics like ABS and PLA. While easy to use, FDM’s limitations include a moderate resolution (★★☆☆☆) and surface finish (★★☆☆☆), making it ideal for simpler designs.
CNC Tools:
CNC machining is highly valued for its precision and versatility, particularly for structural parts and metal components, providing exceptional resolution, accuracy, and surface finish (all ★★★★★). With materials ranging from plastics and soft metals to wood, stone, and glass, CNC tools can handle demanding projects, though their ease of use is rated moderate (★★★☆☆) due to setup complexity. CNC machine prices vary widely, with small CNC tools starting around $2,000, engravers available for less than $500, and more advanced tools like water jet cutters starting at $20,000.
Each of these tools has distinct applications and advantages, allowing for flexibility based on prototype requirements and budget. For larger, more complex prototypes, SLS and CNC provide engineering-grade results, while SLA and FDM are excellent for quick, cost-effective prototypes.
Rapid Prototyping Services vs. In-House Rapid Prototyping
When comparing Rapid Prototyping Services vs. In-House Rapid Prototyping, Leanplans stands out by addressing some of the main limitations traditionally associated with outsourcing. Unlike many service providers, Leanplans offers both competitive pricing and significantly reduced lead times, transforming what is usually considered a drawback in outsourced prototyping into a key advantage.
Leanplans achieves this by maintaining a highly optimized supply chain and leveraging advanced automation in processes, ensuring that parts are not only produced efficiently but also delivered swiftly—often at speeds competitive with in-house 3D printing setups. Additionally, our range of cutting-edge additive and subtractive technologies, along with rapid tooling options, gives clients flexibility in materials and finishes that are hard to achieve with a single in-house 3D printer.
With Leanplans, customers can take advantage of scalable production and expert guidance on material selection and design modifications, all while keeping project timelines on track and minimizing prototyping expenses. This means that whether you’re ordering a single prototype or a low-volume production run, Leanplans delivers the benefits of rapid prototyping without the typical outsourcing trade-offs.
Get a Free Quote!
Leave your contact details, or directly visit our online quoting platform to experience the future of material selection and production. Get expert material evaluations, tailored DFM analysis, and fast 24-hour production turnaround.
- Free Quote: Upload your designs, and our AI-powered engine will generate a custom quote in seconds.
- Talk to an Expert: Connect with one of our engineers via WhatsApp for immediate assistance.